Concrete Crew Denton TX follow a series of steps to prepare the worksite, taking into account factors such as site layout, ground conditions, formwork installation, and safety considerations.
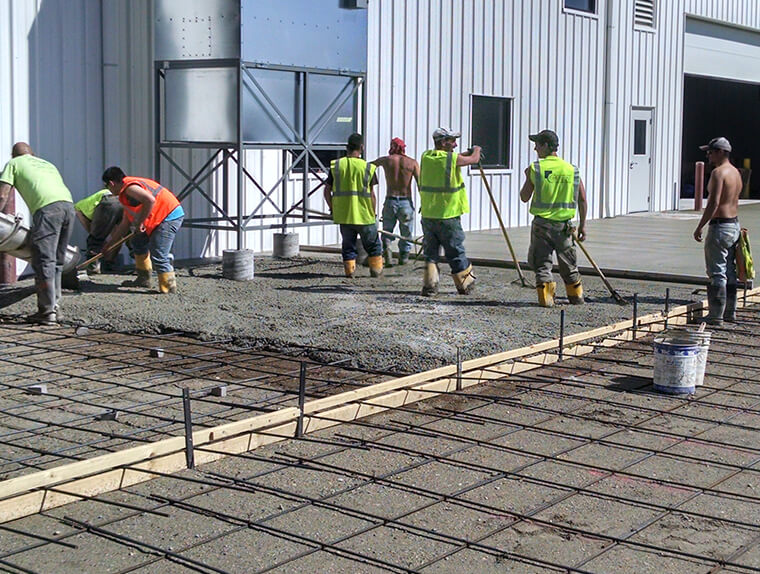
Here’s a comprehensive guide on how concrete crews prepare a worksite for pouring concrete:
- Site Assessment and Planning:
- Before starting any work, the concrete crew conducts a thorough assessment of the site to identify potential hazards, obstacles, and logistical challenges. They review construction plans, specifications, and drawings to understand the layout, dimensions, and requirements of the concrete pour.
- The crew plans the sequence of work, including the location of access routes, staging areas for materials and equipment, and placement of formwork and reinforcement. They consider factors such as site access, terrain, drainage, and nearby structures to optimize workflow and ensure safe and efficient operations.
- Clearing and Grading:
- The first step in preparing the worksite is to clear the area of any debris, vegetation, or obstacles that could interfere with the concrete pour. This may involve removing rocks, roots, trash, and other debris from the site.
- The crew then grades the ground to create a level and uniform surface for the concrete pour. This may involve using grading equipment such as bulldozers, graders, or skid-steer loaders to adjust the elevation and slope of the site to meet project specifications.
- Layout and Marking:
- Next, the crew lays out the dimensions and boundaries of the concrete pour using stakes, string lines, and marking paint. They mark the perimeter of the pour area, as well as any edges, corners, or reference points indicated in the construction plans.
- The layout ensures that the concrete is poured to the correct dimensions and alignment, preventing errors or deviations that could compromise the integrity of the structure. The crew double-checks the layout for accuracy before proceeding to the next step.
- Installation of Formwork:
- Formwork, also known as molds or shuttering, is used to contain and shape the concrete during pouring. The crew installs formwork along the perimeter of the pour area, following the layout and marking established earlier.
- Formwork may be made of wood, metal, or plastic, depending on the size, shape, and complexity of the concrete structure. The crew assembles the formwork panels, ties them together securely, and braces them to withstand the pressure of the concrete.
- Care is taken to ensure that the formwork is aligned, leveled, and properly supported to prevent leaks, bulges, or misalignment during the concrete pour. Expansion joints or control joints may be installed as needed to accommodate thermal expansion and contraction of the concrete.
- Reinforcement Installation:
- In some cases, reinforcement such as rebar or wire mesh may be required to strengthen the concrete and prevent cracking. The crew installs the reinforcement according to the specifications and details provided in the construction plans.
- Rebar is typically placed in a grid pattern within the formwork, with spacers or chairs used to maintain the proper spacing and elevation. Wire mesh may be laid on top of the base layer of concrete before pouring additional layers.
- The crew ensures that the reinforcement is positioned correctly and securely tied or fastened in place to provide adequate support and structural integrity.
- Preparation of Access Routes and Equipment Placement:
- The crew establishes access routes for concrete trucks, pumps, and other equipment to reach the pour area safely and efficiently. This may involve clearing paths, removing obstacles, and leveling the ground to provide a stable surface for vehicle traffic.
- Concrete trucks are positioned strategically to minimize travel distances and facilitate continuous pouring without interruptions. Pump trucks or conveyors may be used to transport concrete to hard-to-reach areas or elevated surfaces.
- Equipment such as mixers, vibrators, and finishing tools are set up near the pour area for easy access and use during the concrete placement and finishing process.
- Safety Precautions:
- Throughout the worksite preparation process, the crew prioritizes safety by implementing appropriate safety measures and protocols. This includes providing personal protective equipment (PPE) such as hard hats, safety glasses, gloves, and steel-toed boots to all crew members.
- Safety barriers, signage, and barricades are erected to delineate hazardous areas and restrict access to unauthorized personnel. Fall protection measures are implemented for work performed at heights, and traffic control measures are implemented to ensure the safety of workers and pedestrians in the vicinity of the worksite.
- Final Inspection and Readiness Check:
- Before proceeding with the concrete pour, the crew conducts a final inspection of the worksite to ensure that all preparations have been completed satisfactorily. They verify that formwork is securely in place, reinforcement is correctly positioned, and access routes are clear for concrete delivery.
- Any issues or concerns identified during the inspection are addressed and resolved promptly to minimize delays and disruptions. Once the crew is satisfied that the site is ready, they proceed with the concrete pour according to the established plan and schedule.
Proper worksite preparation sets the foundation for a successful Concrete Crew Denton TX project, leading to high-quality results and satisfied clients.
Denton Concrete Crew
1901 Lakeview Blvd, Denton, TX 76208, United States
1-940-461-7177